Main content
How to make an iconic £4,000 Wedgwood vase
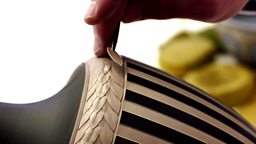
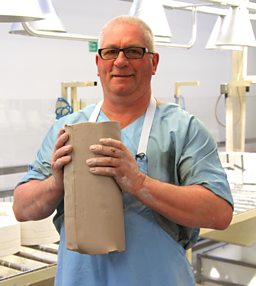
It all begins with a lump of clay.
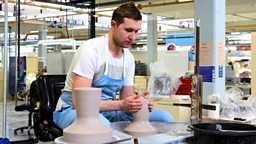
Chris Mottram, Thrower. The clay is shaped on a potter’s wheel, a skill that has been passed down from potter to potter.
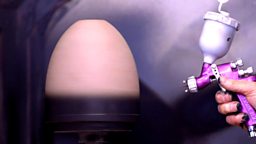
The vase is sprayed with a surface coating of colour before the turner carefully reveals the base colour underneath.
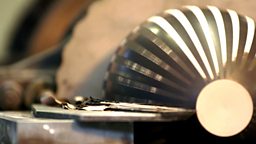
The process of putting the stripes into the Panther Vase dates back to 1764 and is still done exactly the same way today. The turner turns the wheel by hand slowly and it pulls the base closer to cut through the colour, revealing the base below. The tool is adjusted to fine tune and the process is repeated.
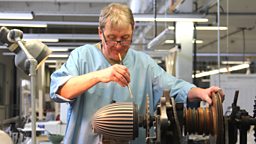
Neil Burton has worked as a Turner at Wedgwood for 44 years. Here he is applying adhesive to attach the neck of the vase to the base.
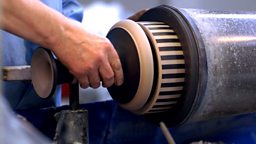
Neil must work quickly as he only has a 10 second window to fix the neck to the base before the adhesive dries.
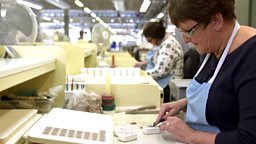
Susan Green, Figure Maker. Sue has worked as a Figure Maker at Wedgwood for 45 years. The clay is rolled, knocked into moulds and pressed, the excess clay is then scraped off before the leaves are coaxed out.
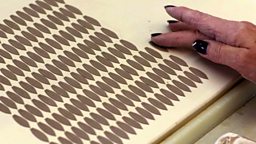
There are 160 leaves on one Panther Vase. They are placed on a damp mat until the Ornamenter is ready to use them.
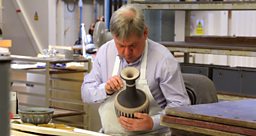
Kevin Dodd, Ornamenter. Each leaf is patiently placed on the vase by the Ornamenter.
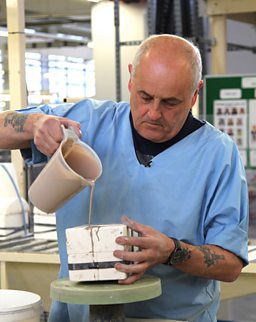
Jeff Pettitt, Caster. Liquid clay is poured into a mould to make the trademark Panther figurines that give the vase its name.
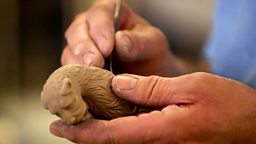
Adhesive is applied to the Panther figurine to attach it to the vase.
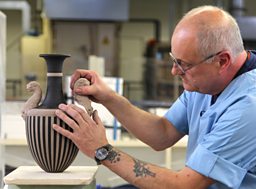
The panther figurines are carefully attached.
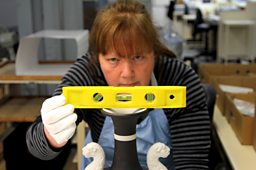
Every detail is checked to ensure it’s perfect.
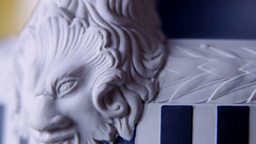
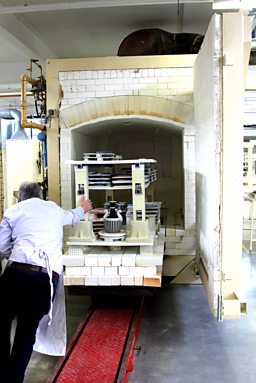
The vase is finally fired in a kiln at 1180 degrees for 18 hours and then cooled for a further 12-14 hours.
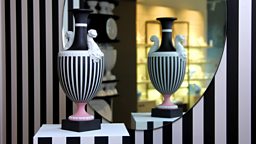